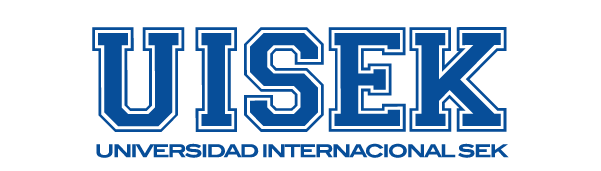
Por favor, use este identificador para citar o enlazar este ítem:
https://repositorio.uisek.edu.ec/handle/123456789/4221
Título : | Optimización del sistema de precalentamiento de crudo de carga mediante el aprovechamiento del calor residual de los productos obtenidos de la unidad no catalítica mediante el diseño de un intercambiador de calor de crudo carga-jet fuel para reducir costos operativos en la producción de productos limpios en la refinería de Lago Agrio |
Autor : | Rubio Aguiar, Rodolfo Jefferson Orellana Sáenz, Daniel Fernando |
Palabras clave : | EFICIENCIA ENERGÉTICA PETRÓLEO ENERGÍA INDUSTRIALIZACIÓN PRODUCCIÓN HORNO |
Fecha de publicación : | mar-2021 |
Editorial : | Universidad Internacional SEK |
Citación : | CT-MECI O668op/2021 |
Resumen : | Hydrocarbons (Oil + Gas), are organic compounds that contain carbon and hydrogen, occurring in nature as gases, liquids, fats and sometimes solids. Hydrocarbons are an important source of energy generation for industries, for our homes and for the development of our daily lives. But they are not only fuels, but through more advanced processes their elements are separated and their use is achieved through the petrochemical industry. The petrochemical industry has multiplied the use of oil in the manufacture of different objects made of plastic and synthetic fibers. Many things that surround us as pens, the fabric of bath clothes, creams, paints, insecticides, many parts of machines and appliances, and even the petrochemical soda bottles to exist. But the most important thing about refining is to obtain gasoline and distillates. The hydrocarbon industry is very fluctuating due to the different political and socio-economic factors that influence its cost per barrel, which is why the best way to guarantee the return on our investment is by lowering the operating cost, this can be done by optimizing resources, taking advantage of resources opportunities for improvement and improving processes. In Oil block 56, located in the Province of Sucumbíos - Nueva Loja, Petroamazonas Ep has the Lago Agrio Refinery, which has an atmospheric distillation unit where 1000 barrels of oil are processed per day (BPD). In its subdivision four streams are obtained which are: base gasoline, jet fuel, diesel and reduced crude, as derived products. The outgoing diesel current with an approximate temperature of 183 ° C due to its separation in the fractionation tower in the direction of a stripper and air cooler has sensible heat that is not used in another operation giving this heat to the environment. Waste energy wasted in this type of process could increase operating costs; consequently, the need is generated to carry out the thermal design of a “crude load / diesel” exchanger to take advantage of the heat produced by diesel cooling using a shell and tube exchanger. The recovered heat will be used in a first preheating of crude load for the process of separation and obtaining of derivatives. The future implementation of this work leads to a decrease in the volume of gasoline consumed in the heating furnace and therefore to a saving of this fuel, which will be reflected in the final cost per gallon of derivative produced in the plant. This is important in order to improve the energy efficiency of the process. The fraction of Jet Fuel or Kerosene that leaves the distillation unit at a mass flow of 1400 lb / hour enters the heat exchanger at approximately 350 ° F, on the other hand, in counter flow the crude enters the load approximately 11538 lb / hour at a temperature of 80 ° F, after the heat exchange the kerosene uses its energy until it reaches the outlet temperature of the exchanger of 130 ° F, thus increasing the temperature of the crude oil load to 120 ° F. For this exchanger with Crude - Kerosen fluids the global heat transfer coefficients vary between 10 Btu / h ft2 ° F to 35 Btu / h ft2 ° F. This global heat transfer coefficient for the current design was calculated at 10.10 Btu / h ft2 ° considering the fouling factors of the crude oil load 0.005 h ft2 ° F / Btu and the kerosene 0.001 h ft2 ° F / Btu. It was calculated that the required area for heat exchange is 176 square feet, from there the design is made with a number of tubes of 44 and a length of 16 feet per tube, the number of tubes was considered with the space available in the refinery For the implementation, it is recommended that the length of the tubes be equal to half the available space, in order to facilitate the installation and cleaning of the tube bundle. To increase the heat transfer coefficient on the tube side, we try to have the highest possible speed in this case we have a speed of 3 ft / s, this is achieved by using the largest number of tubes that allows the design with the smallest internal diameter. of pipes possible, this depending on the type of fluid we have on the pipe side, if it is a fluid with a high fouling coefficient it is not recommended to use diameters smaller than 1 inch, in addition, the limitation due to the pressure drop in In this case, due to the fouling coefficient of the crude oil, a 1-inch tube was considered. Regarding the Reynolds number, we need the fluid to be as turbulent as possible, this will favor heat exchange by increasing the values of the transmission coefficients on both the tube side and the shell side, this Reynolds number will increase as we reduce the size of the tubes or the shell, but it should also be taken into account that very small diameters can cause clogging problems when working with fluids with high fouling coefficients, reducing efficiency considerably. The results obtained from the calculation and simulation indicate a heat transfer area of 176 square feet, the exchanger is designed with 44 tubes with a shell diameter of 12 inches and a length of tubes of 16 feet with an outer diameter of tubes of 1 inch and the tube spacing is 1.25 inches. Regarding the temperatures of the hot fluid (Jet fuel), it enters the exchanger at a temperature of 350 ° F and leaves after the heat exchange at a temperature of 130 ° F. The fluid to be heated or cold (crude) enters at a temperature 80 ° F and exits the exchanger at a temperature of 120 ° F. The global coefficient of heat exchange required is 9.63 Btu / h ft² ° F and according to design the global coefficient calculated is 10.10 Btu / h ft² ° F. In the economic analysis, we determined that with the implementation of the heat exchanger we reduced the amount of fuel required for the furnace by 140 gallons per day, that is, approximately 4404.38 Kw / h per day, which represents a saving of 114,975 dollars per year. The implementation of this work leads to a decrease in the volume of gasoline consumed in the heating furnace and therefore to a saving of this fuel, which will be reflected in the final cost per gallon of derivative produced in the plant, which is important. in order to improve the energy efficiency of the process. |
Descripción : | El petróleo es una mezcla de varios componentes en los cuales prevalecen los hidrocarburos, estos pueden estar en estado líquido, semi solido o gaseoso. Los hidrocarburos son una fuente importante de generación de energía a nivel mundial y para casi todas las industrias y hogares. Pero no son sólo combustibles, sino que a través de procesos más avanzados se separan sus elementos y se logra su aprovechamiento a través de la industria petroquímica. La industria de la petroquímica, ha multiplicado el uso del petróleo en la fabricación de polimeros y fibras sintéticas. Casi todo los productos que se utilizan en la vida diaria son hechos en base a hidrocarburos como son combustibles, plásticos, lapiceros, muchas telas, las cremas, las pinturas, los insecticidas, muchas partes de las máquinas y de los electrodomésticos entre otros. Para obtener estos productos derivados, el petróleo crudo debe pasar por varios procesos (catalíticos y no catalíticos), en los procesos no catalíticos se obtiene productos básicamente por incrementos de temperatura y variaciones de presión, en los procesos catalíticos se utilizan diferentes catalizadores que básicamente son sustancias que se añaden al proceso para aumentar la velocidad de reacción sin ser consumida en el proceso. En el bloque 56, ubicado en la Provincia de Sucumbíos cantón Nueva Loja, la empresa Petroamazonas EP cuenta con la Refinería Lago Agrio, la cual tiene una unidad no catalítica o destilación atmosférica (NC-1) la cual tiene una capacidad de procesamiento de 1000 barriles de petróleo por día (BPD). Esta unidad fracciona el crudo carga en diferentes corrientes según la curva de destilación del crudo en: Gasolina base Jet fuel Diésel Crudo reducido La unidad de destilación atmosférica de la refinería de Lago Agrio es poco eficiente en su proceso, esto debido a que se desperdicia mucha energía térmica en las corrientes de productos limpios obtenidos, esta energía puede ser aprovechada y así reducir el consumo de combustibles fósiles (gasolina) para el calentamiento del crudo carga. Estos productos a su salida de la torre de destilación atmosférica conservan aun mucha energía la cual actualmente es desperdiciada en procesos de enfriamiento y condensación para su posterior almacenamiento. Esta energía se aprovechará con este sistema de precalentamiento del crudo carga mediante la implementacion de un intercambiador de calor.La fracción de Jet Fuel o Keroseno que sale de la unidad de destilacion a un flujo masico de 1400 lb/hora ingresa aproximadamente a una temperature de 350° F al intercambiador de calor, por otra parte en contra flujo ingresa el crudo carga aproximadamente 11538 lb/hora a un temperatura de 80°F, después del intercambio de calor el Keroseno sede su energía hasta llegar a la temperatura de salida del intercambiador de 130°F, incrementando así la temperatura del crudo carga a 120°F. Para este intercambiador con fluidos Crudo – Kerosen los coeficientes globales de transferencia de calor varian entre 10 Btu/h ft2 °F a 35 Btu/h ft2 °F. Este coeficiente global de transferencia de calor para el actual diseño se calculó en 10.10 Btu/h ft2 ° considerando los factores de ensuciamiento del crudo carga 0.005 h ft2 °F/Btu y del Keroseno 0.001 h ft2 °F/Btu. Se calculó que el área requerida para el intercambio de calor es de 176 pies cuadrador de ahí se realiza el diseño con numero de tubos de 44 y una longitud de 16 pies por tubo, el numero de tubos se consideró con el espacio disponible en la refineria para la implementación, se recomienda que el largo de los tubos sea igual a la mitad del espacio disponible, con el fin de facilitar la instalación y limpieza del haz de tubos. Para incrementar el coeficiente de transferencia de calor del lado tubos, se procura tener la velocidad más alta posible en este caso tenemos una velocidad de 3 ft/s, esto se logra usando el mayor número de tubos que permite el diseño con el menor diámetro interno de tubos posible, esto dependiendo del tipo de fluido que tengamos en el lado tubos, si es un fluido con un coeficiente de ensuciamiento alto no se recomienda utilizar diámetros menores a 1 pulgada además se debe tener en cuenta la limitación por la caída de presión en este caso debido al coeficiente de ensuciamiento del crudo se consideró un tubo de 1 pulgada. En cuanto al numero de Reynolds necesitamos que el fluido sea lo mas turbulento posible, esto favorecerá el intercambio de calor incrementando los valores del coeficientes de transmisión tanto del lado tubo como del lado carcaza, este numero de Reynolds se incrementara a medida que reducimos el tamaño de los tubos o la coraza, pero también se debe tener en cuenta que los diámetros muy pequeños pueden generar problemas de taponamientos cuando se trabaja con fluidos con coeficientes de ensuciamiento altos reduciendo la eficiencia considerablemente. En el análisis económico determinamos que con la implementación del intercambiador de calor reducimos la cantidad de combustible requerido para el horno en 140 galones por día es decir aproximadamente 4404.38 Kw/h al día, lo que representa un ahorro de 114 975 dolares al año. La implementación de este trabajo, conduce a una disminución del volumen consumido de gasolina en el horno de calentamiento y por ende a un ahorro de este combustible, que se reflejará en el costo final por galón de derivado producido en la planta, lo cual es importante con el fin de mejorar la eficiencia energética del proceso. |
URI : | https://repositorio.uisek.edu.ec/handle/123456789/4221 |
Aparece en las colecciones: | Maestría en Ecoeficiencia Industrial |
Ficheros en este ítem:
Fichero | Descripción | Tamaño | Formato | |
---|---|---|---|---|
Orellana Sáenz Daniel Fernando.pdf | 2,93 MB | Adobe PDF | Visualizar/Abrir |
Los ítems de DSpace están protegidos por copyright, con todos los derechos reservados, a menos que se indique lo contrario.